一、设备完好率
设备完好率也区分A类设备、B类设备、C类设备,在智慧水务行业中,对于A类设备的完好率是要求非常高的。
所谓完好设备一般标准是:
①设备性能良好,如机械加工设备的精度达到工艺要求;
②设备运转正常,如零部件磨损、腐蚀程度不超过技术规定标准,润滑系统正常、设备运转无超温、超压现象;
③原料、燃料、油料等消耗正常,没有油、水、汽、电的泄漏现象。对于各种不同类型的设备,还要规定具体标准。例如传动系统的变速要齐全、滑动部分要灵敏、油路系统要畅通等。
公式中的设备总台数包括在用、停用、封存的设备。在计算设备完好率时除按全部设备计算外,还应分别计算各类设备的完好率。
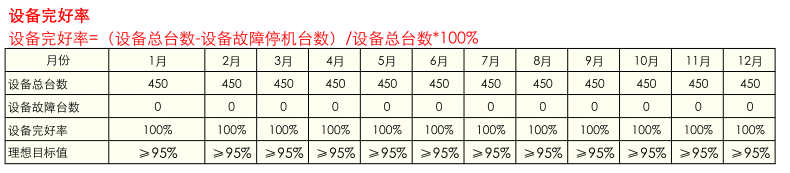
二、设备利用率
定义:设备利用率是指每年度设备实际使用时间占计划用时的百分比。是指设备的使用效率。是反映设备工作状态及生产效率的技术经济指标。
在一般的企业当中,设备投资常常在总投资中占较人的比例。因此,设备能否充分利用,直接关系到投资效益,提高设备的利用率,等于相对降低了产品成本。所以,作为企业的管理者,在进行生产决策的时候,一定要充分认识到这一点。
一般包括:设备数量利用指标——实有设备安装率,已安装设备利用率;设备时间利用指标——设备制度台时利用率,设备计划台时利用率;设备能力利用指标——设备负荷率;设备综合利用指标——设备综合利用率。
过去,设备利用率一般仅指设备制度台时利用率。
计算公式:
公式一
设备利用率 = 每小时实际产量 / 每小时理论产量 x 100%
公式二:
设备利用率 = 每班次(天)实际开机时数 / 每班次(天)应开机时数 x 100%
公式三:
设备利用率 = 某抽样时刻的开机台数 / 设备总台数 x 100%
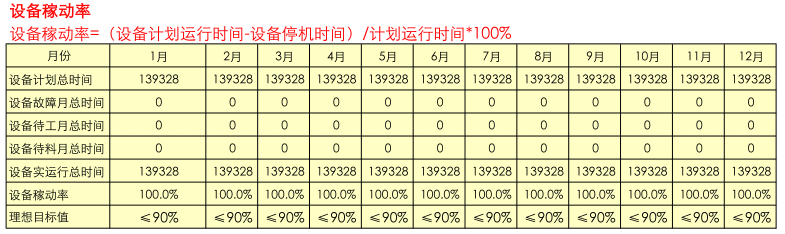
三、设备故障率
定义:设备故障率是指事故(故障)停机时间与设备应开动时间的百分比是考核设备技术状态、故障强度、维修质量和效率一个指标。
计算公式:故障造成的停机时间 / 设备工作运行时间 x 100%
在污水公司、自来水公司、化工厂这都是一个非常重要的考核指标。
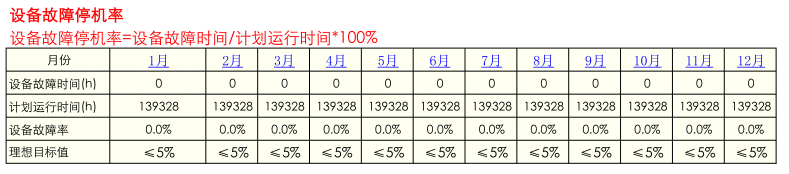
四、设备综合效率OEE
TPM管理体系主张以设备综合效率来度量企业的设备管理水平。
定义:设备综合效率(overall equipmenteffectiveness,即OEE)其本质是实际合格产量与负荷时间内理论产量的比值。
设备综合效率考核的核心思想是:一条生产线的实际可用时间只占计划运行时间的一部分,其中可能只发挥了设备部分的性质,而且可能只有部分产品是合格品。
按照国际统一的标准,一个合格的制造业,其设备综合效率的指标应大于85%。从目前国内企业不完全统计资料来看,尽管不同行业的设备综合效率差别较大,但总体来说,仍处于较低的水平,设备综合效率大约在70%左右。
每一个生产设备都有自己的最大理论产能,要实现这产能必须保证没有任何干扰和质量损耗。当然,实际生产中是不可能达到这一要求,由于许许多多的因素,不问设备存在着大量的失效;例如出过设备的故障,调整以及设备的完全更换之外,当设备的表现非常低时,可能会影响生产率,产生次品,返工等。
计算公式:
设备综合效率=时间开动率×性能开动率×合格品率×100%
时间开动率反映了设备的时间利用情况;
性能开动率反映了设备的性能发挥情况;
合格品率则反映了设备的有效工作情况。
反过来,时间开动率度量了设备的故障、调整等项停机损失,性能开动率度量了设备短暂停机、空转、速度降低等项性能损失;合格品率度量了设备加工废品损失。

A.时间开动率的计算
一些日韩企业把开动率称为稼动率,事实上就是我国企业用的开动率,时间开动率的计算公式是:时间开动率 = 开动时间/负荷时间
负荷时间 = 计划设备用于生产的时间
开动时间 = 设备实际进行生产的时间
设备调整初始化时间包括更换产品规格、更换工装模具等活动所用时间。
例如,某设备计划生产时间为8小时(480分钟),实际运行时间为6小时(360分钟),则可用性为360/480 = 0.75,即75%。
B.性能开动率的计算
性能开动率的计算是整个设备综合效率计算的关键,很多企业设备综合效率计算出现偏差,大多数情况都是计算性能开动率出现的错误导致的。其计算公式如下:
性能开动率 = 净开动率 × 速度开动率
净开动率 = 加工数量 x 实际加工周期/开动时间
速度开动率 = 理论加工周期/实际加工周期
性能开动率反映了实际产品所用时间与开动时间的比例。它的高低反映了生产中的设备空转损失、无法统计的小停机损失。性能开动率也可以用另外一种算法,即:
性能开动率 = 理论加工周期 × 加工数量/开动时间
上式中,由于加工数量、开动时间等都可以计算出来,因此要获得相对比较准确的性能开动率,其关键在于获得较为准确的理论加工周期,即设备制造公司标明的或是设备设置在*状态下的生产单位产品所需要的时间。
一般情况下,理论加工周期的确定原则是:
(1) 设备初始说明书上记录的时间;
(2) 如果设备初始说明书上没有记录理论加工周期,或现在运行设备加工周期比记录上的理论加工周期快,在这种情况下,以测定的x时间为准;
(3) 在设备已更新改造的情况下,以改造后的x时间定为标准。
C.合格品率的计算
合格品率的计算可以用下面的公式来表示:
合格品率 = 合格品数量/加工数量
在实际应用中,不同行业对合格品的界定是不同的。比如一些石油化工行业,不同标号的成品油可以通过勾兑成为合格品;一些钢铁行业的不合格品,则又可细分为降级、返工和简单修复后合格等;而对于生产流水线,不同企业合格品率的统计工序也各不相同。因此,即使计算合格品率,也要在企业内部制定统一的计算方法和标准。
如果追究设备综合效率的本质内涵,其实就是计算周期内用于加工的理论时间和负荷时间的百分比,即:
设备综合效率 = (理论加工周期×合格产量)/负荷时间 = 合格产品的理论加工总时间/负荷时间
也就是实际产量与负荷时间内理论产量的比值。
举例
某工厂实施8小时作业体制,其中中午休息1小时,上班时间包括早会,检查,清扫等20分钟,上、下午期间各休息15分钟。
有一台设备,因应市场需要,每天加班30分钟,该设备理论节拍为0.8分钟,在正常稼动时间内应生产575件,但实际仅生产出418件,实际测得的节拍为1.1分钟,当天更换刀具及故障停机时间为70分钟。
不良率维持2%。
请问该设备的设备综合效率为多少?
A: 实际作业时间 =480+30=510min
B: 计划停止时间 50min
C: 负荷时间 510-50=460min
D: 停机损失时间 70min
E: 稼动时间 C-D=390min
G: 生产量418件
H: 良品率 98%I:理论节拍0.8
时间开动率 = (460-70)/460 = 84.8%
性能开动率 = (0.8*418)/390 = 85.7%
合格品率 = 98%
于是得到 OEE = 84.8% ×85.7%×98% = 71.2%